Flexo Platemaking Has Never Been This Straightforward
Printing professionals face unprecedented challenges when considering investments in flexo platemaking. As a trailblazer in the industry, Esko recognizes these challenges and offers innovative flexo platemaking solutions that empower customers to stay ahead in a competitive market.
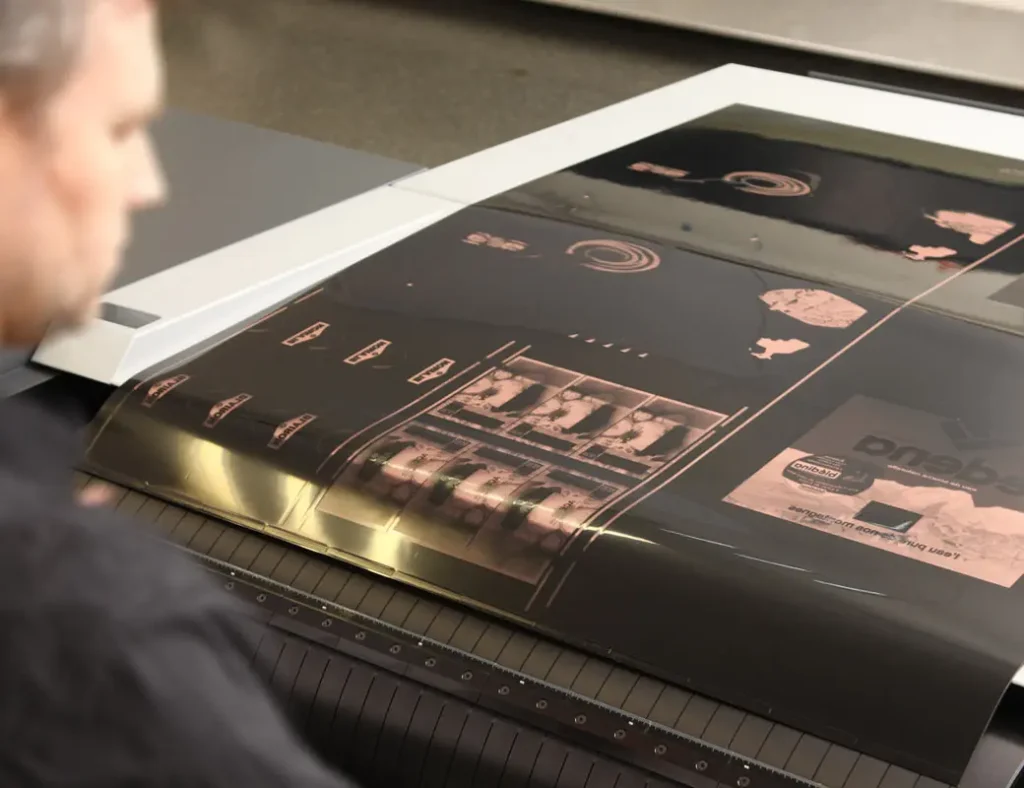
Overcome the Challenges of Flexo Platemaking
Inefficient Processes
Inefficient processes in the platemaking workflow extend lead times for print professionals, making it harder to meet tight deadlines and sustain a competitive edge.
Cost-Inefficiencies
It’s important for printing professionals to cut costs while minimizing waste and reducing manual interventions. Finding that perfect balance without sacrificing quality is not without its challenges.
Labor Shortages
Labor shortages pose a challenge to operational efficiency and timely production in flexo platemaking processes.
Sustainability
Print professionals are under increasing pressure to adopt sustainable practices. However, it’s not always easy to optimize materials, reduce waste, and minimize energy consumption.
Complexity of Print Jobs
Print service providers often encounter myriad print job complexities, ranging from intricate designs to diverse substrates.
Print Quality
Attaining impeccable print quality is imperative. However, ensuring high-resolution imaging and precise plate exposure demands careful consideration.
A Scale for Superior Flexo Quality
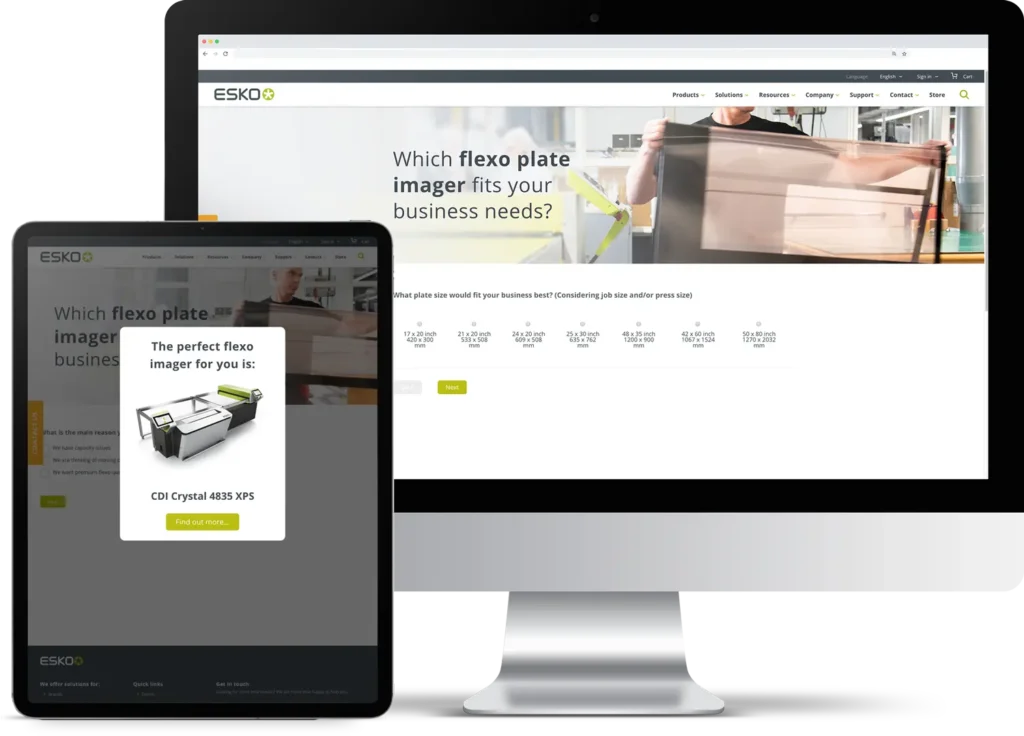
Find the Right Flexo Imager for You
Use this handy quiz to find the flexo imager that perfectly matches your company’s needs.
Esko Is the Only Independent Expert that Covers the Entire Scope of Flexo Platemaking
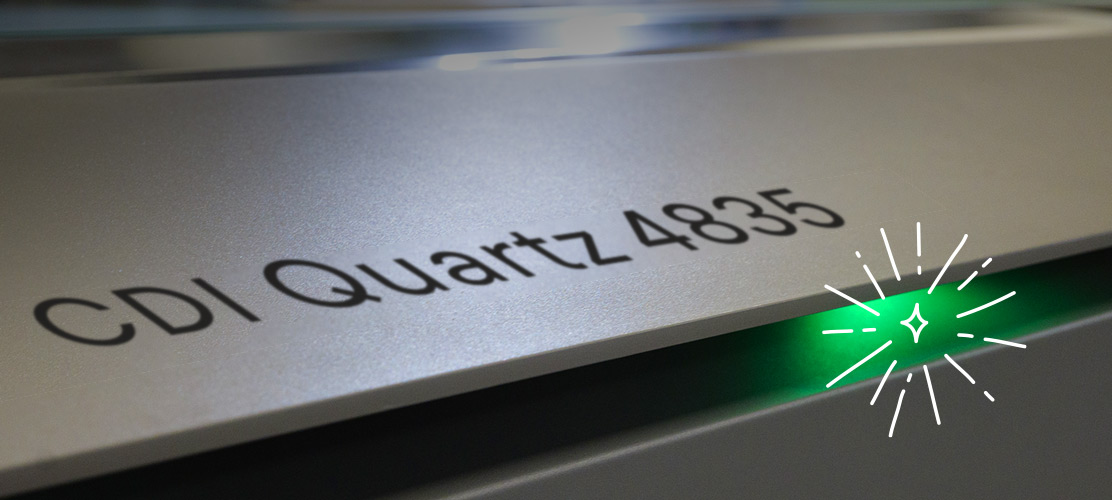
CDI Quartz
Market-Leading Flexo Print Quality
Produce the most accurate and best quality plates, reduce ink usage to deliver the absolute best quality final print.
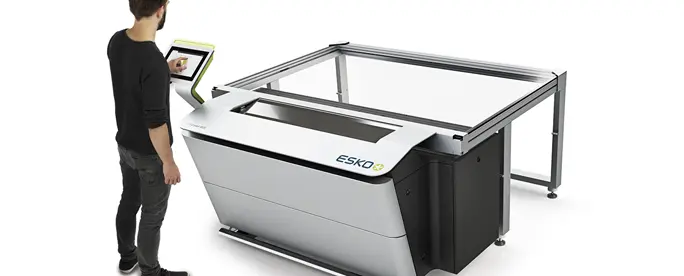
CDI Crystal
Flexo Plate Imaging
Create flawless plates that excel in high print output and press stability.
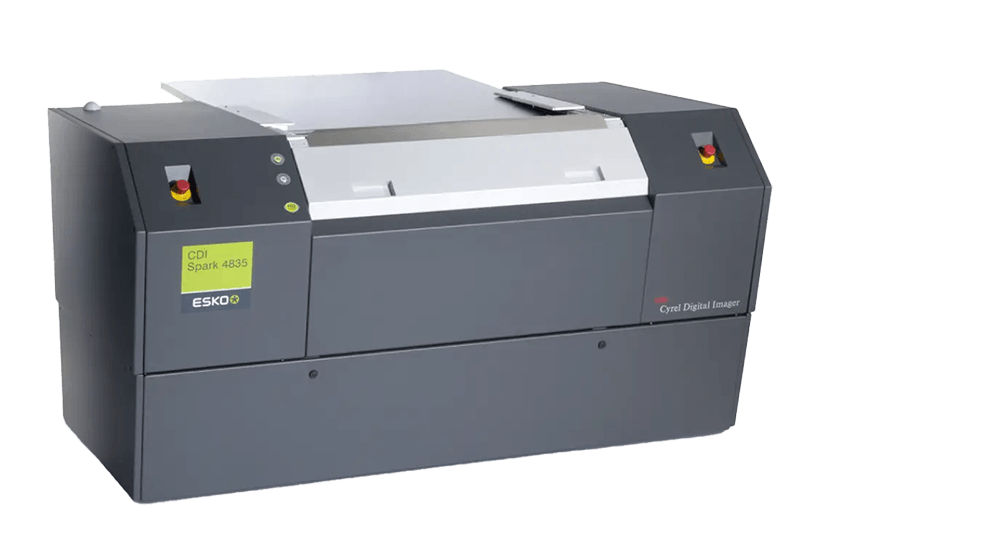
CDI Spark & Advance
Flexo Plate Imagers
Caters to small & large plates, tag & label, flexible packaging, folding carton, & corrugated segments.
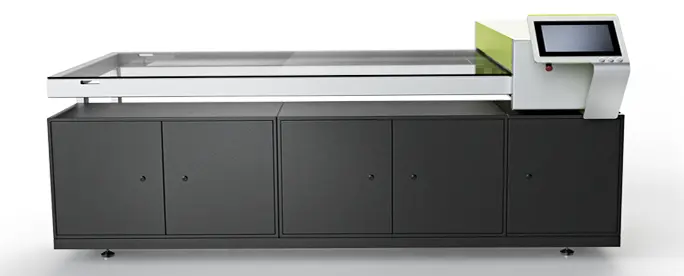
XPS Crystal
Flexo Plate Exposure Unit
Unlock the ability to produce highly consistent digital flexo plates, every time.
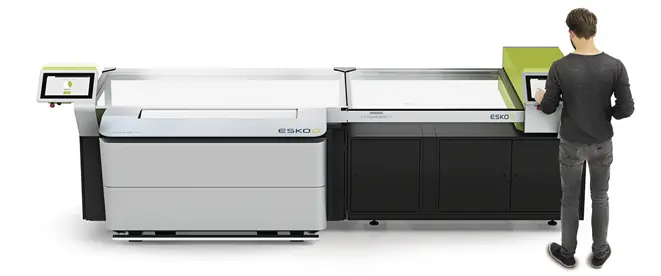
CDI Crystal XPS
Combined Flexo Plate Imager and Exposure Unit
Get the perfect, consolidated flexo platemaking workflow.
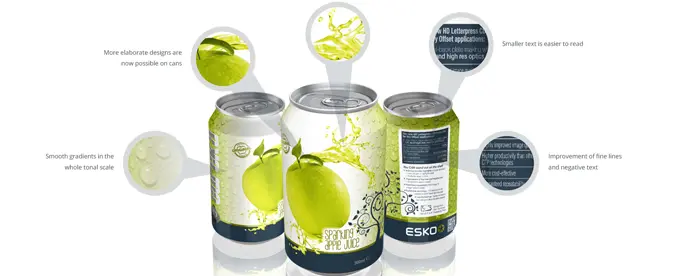
HD Letterpress
Imaging for Metal-Backed Plates
Tackle dry offset printing challenges and ensure smooth highlights and precise linework.
Featured Resources
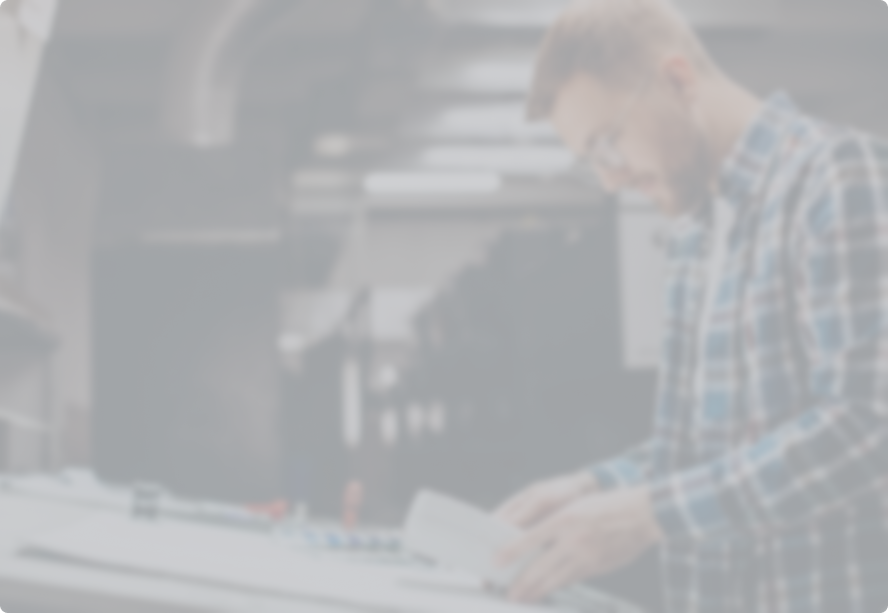
An Advanced Look at Screening for Flexography – Webinar Replay
Hear insights from flexo expert, Robert Bruce as he guides us through an advanced look at screening for flexography.
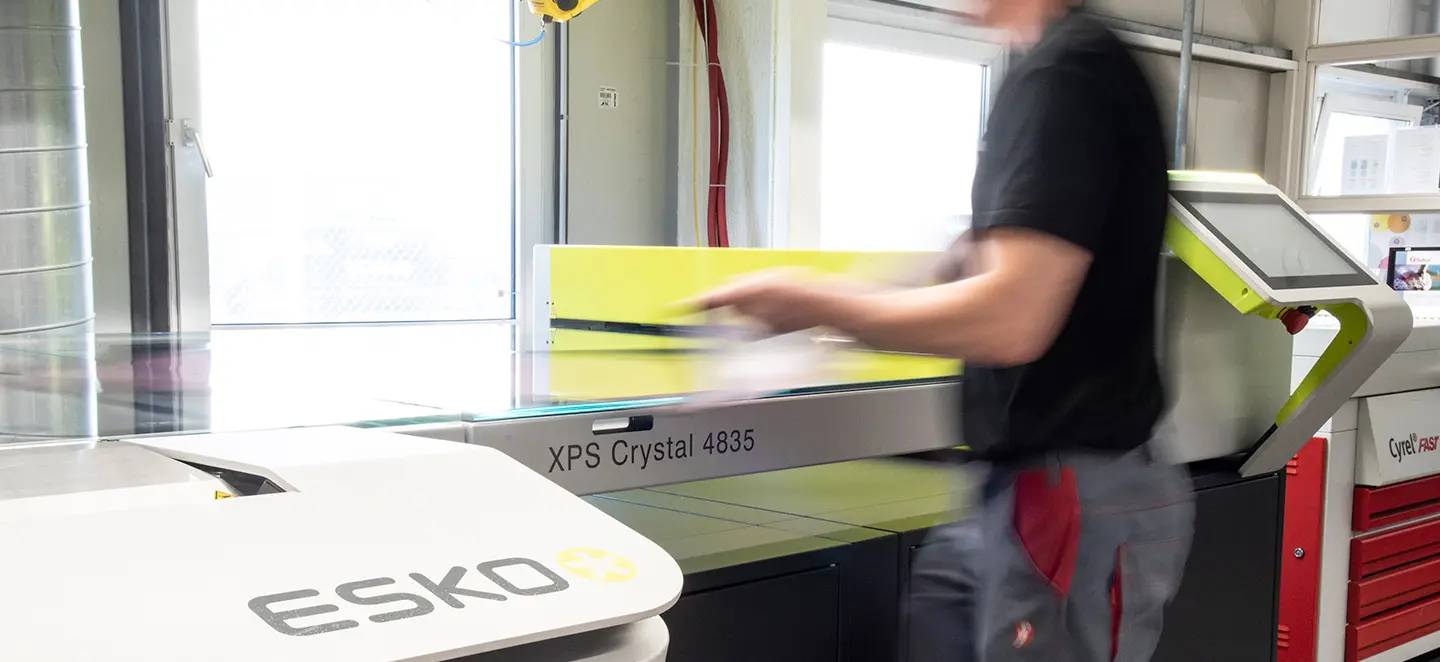
7 Reasons to Work with an Esko Flexo Platemaking Workflow
Learn more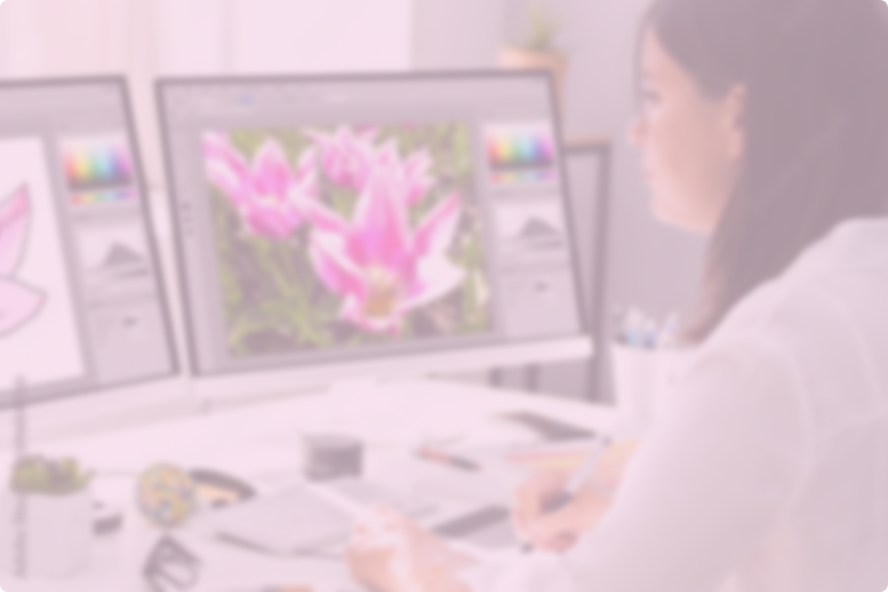
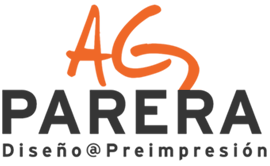