A Long Tradition of Excellence
The company’s Flexographic Division, located in Winchester, KY and Lithographic Division in Harahan, LA have both received HACCP Accreditation. This acknowledgement from the American Institute of Baking International (AIBI) and Guelph Food Technology Centre (GFTC) assures that both plants have suitable, well-defined food safety programs in place. The Food and Beverage industries are key markets for Walle Corporation and its label products, so the HACCP Accreditation is an important distinction for them.
Walle was one of the first to offer flexo label solutions as an addition to its litho label products, and first to introduce 100% computer-to-plate (CTP) digital workflow for both litho and flexo labels. The company continually reinvests to keep its label production technology and equipment at the forefront of innovation and efficiency. Its expertise from this pioneering effort and Esko CTP workflow has ensured a streamlined, state-of-the-art production process that is fast, efficient and accurate.
The Flexographic Operating Division in Winchester, KY can print labels in up to ten colors with 100% eco-friendly water-based inks, on its high-speed wide-web and mid-web roll-fed presses. As part of its complete workflow, Walle had been operating an Esko Cyrel Digital Imager (CDI) Spark 4835 (35”x48”) flexo plate imager since 2003. It was working well, but recently the company decided it was time to upgrade to a larger imager, and purchased an Esko CDI Spark 4260 (42”x60”) imager outfitted with HD Flexo technology.
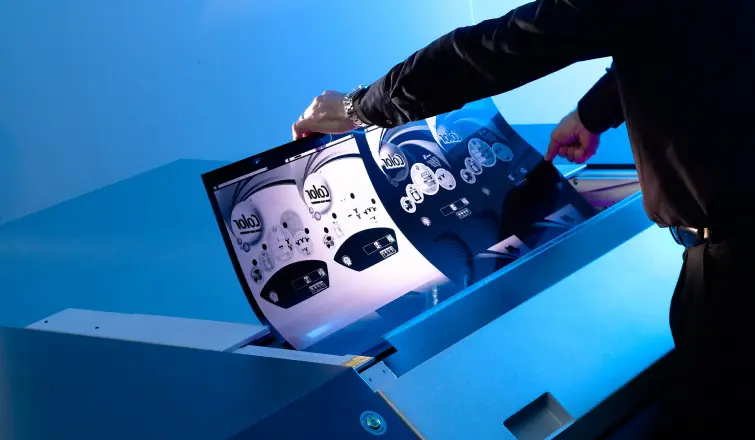
Pushing the Dots
“We’re a progressive company, and had been using stochastic screening for much of our work. But we are always looking for ways to improve,” remembers Jim Combs, Walle Winchester, KY general manager. “We were evaluating with our EskoArtwork representative about a larger CDI to better suit our plate requirements. When they presented their new HD Flexo technology, we included it in our investigation and analysis. Very quickly, we decided that we would invest in the HD Flexo option for our CDI at the same time.”
HD Flexo is a system that combines 4,000 dpi HD laser optics along with unique screening technologies. The high-resolution optics deliver an accurate, sharper imaging of text and line art along with more clearly defined, better shaped screen dots, because the dots are made of more pixels, almost three times more than other devices. The rounder dot shape is more stable on press, resulting in longer print runs with the same printing plate. Utilizing the higher resolution optics and smart screening, HD Screening places both large and small dots in the highlight areas to extend the tonal range to a much smaller percentage value than was previously possible with digital flexo. HD Flexo can image solvent or thermal plates manufactured by a variety of leading plate vendors, in a wide range of plate sizes and formats, without any degradation of quality. This technology is available on all new CDIs, and can also be upgraded on all existing CDI systems.
Now with HD Flexo, everything we print is at 150 lpi, just like our Litho Division. The varying dot size from HD Flexo is equally spaced in the highlights, this allows us to get very fine zero and 1% dots.
Walle’s larger CDI was installed in late October and began imaging traditional plates at first. The HD Flexo installation was completed in mid-November. As typical for any CDI installation, EskoArtwork’s Flexo Implementation Quality program team worked with Walle for three days, optimizing the system, selecting the right pixel size and, according to Combs, “did an excellent job of helping us to transition the old technology to the new. A couple weeks later, DuPont helped us fine-tune the back and main plate exposures. Since then, it’s been smooth sailing.”
Walle found out rather quickly that HD Flexo provided much better highlight reproduction, particularly for those dots below 10%. “The biggest impact we see is where screening highlights fade out to zero – like in drop shadows,” explains Combs. “Now we are more successful reproducing art without the traditional stochastic screening. While we were printing well before, we still had to modify the art we received at times, resorting to tricks to optimize it. Before, we might have modified vignettes some to provide wiggle room to make the screens appear as smooth as possible or adjust the line screen. Now with HD Flexo, everything we print is at 150 lpi, just like our Litho Division. The varying dot size from HD Flexo is equally spaced in the highlights, this allows us to get very fine zero and 1% dots.”
Great Reproduction Brings Financial Reward
Ocean Spray Cranberries, Inc. has been one of Walle’s customers for over 18 years. In each of the last two years, Ocean Spray has recognized Walle with its Supplier of the Year award. “Ocean Spray has always required the highest quality graphics for their labels. At times, some design elements can be more demanding. Nine years ago, going digital flexo noticeably improved graphic reproduction quality. Now, HD Flexo allows us to produce labels with even sharper graphics quality and better dot consistency, resulting in a deeper color in the cranberries, and a smoother reproduction in the vignettes,” comments Combs.
Another big advantage to Walle is that they get consistent reproduction on press. Plate life has been extended in the highlights because HD Flexo uses supporting dots to maintain them. Makereadies have been faster. And, perhaps an overlooked advantage is that Walle no longer makes tweaks on press after a plate is made to achieve the best graphic reproduction. They don’t have to make new plates to overcome a challenging design on press. In fact, Walle has reduced plate costs and has sped up makeready time by 15%.
“We have had a very smooth transition to HD Flexo technology, and it has given us the ability to broaden our scope of business,” concludes Combs. “We are very confident that we can go after—and rival—labels traditionally printed rotogravure. Shrink sleeve labels is our fastest growing segment of our product line. Before we adopted HD Flexo, we had converted a few gravure customers over to flexo already. Now with HD Flexo, we are certain that any label that is currently printed gravure or offset can be reproduced equally well, if not better, with HD Flexo. We know that anything our customers bring us we can reproduce very well without any sacrifice to the original design . HD Flexo has lived up to everything that was promised to us and more.”