Automation Engine and Device Manager
Automation Engine is the core of the system, this will be supplemented with the modules Device Manager and Connect. Currently Automation Engine automates the entire production process, from design to print to cut. Device Manager extends the possibilities thanks to the bi-directional link with the Kongsberg cutting table which allows for better planning and exact time-cost estimates of the cutting process, without an actual test run. Cees Bolijn: “Our new web-shops are relying on pre-flighting (based on pitstop server technology) of PDF documents and the Connect Module makes it possible to easily connect with external parties so outsourcing will be fully integrated in the production workflow.”
Brand owners clearly see the value of versioned and customized signage to address regional, cultural and other differences. The production process used to be quite slow and therefore not cost-effective. With Automation Engine we have overcome this barrier. It enables us to produce products that are completely variable from piece to piece.
Even More Benefits
With Automation Engine Cees Bolijn had already designed dynamic workflows that automate repetitive prepress tasks, thus increasing productivity, reducing operator intervention/errors and saving valuable time, money and materials throughout the production process. The new modules now enable him to complete even more tasks automatically, Cees Bolijn had already achieved this connection with the MIS system developed in-house, enabling automatic job creation and the inclusion of job parameters into the workflow via XML data. In fact jobs will now be linked as XML files to the Automation Engine from the outset. It is a hot folder process, in which each stage is linked to the next, with status reports at each stage.
Cees Bolijn did not install Device Manager, until now. The current ESKO Device Manager software enables him not only to send files to the Kongsberg table for milling and cutting in the finishing stage (which was already possible), but also to retrieve information in advance, for example, to predict how long it will take to finish a file. This in turn enables him to inform his customers about the duration of the overall job and final delivery of ready products. The system is compatible with the new C-series of ESKO Kongsberg cutting tables. In due course it will also be possible with the former tables.
Optimizing the Finishing Workflow
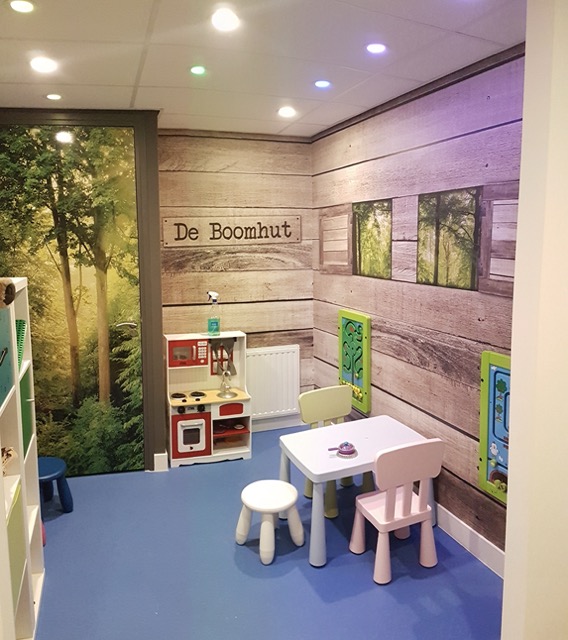
Summarizing these processes, Cees Bolijn related that 6 to 7 years ago his main goal was to optimise the technical aspects associated with printing and finishing. The company employs super wide EFI VUTEk printing equipment and smaller latex and dye sub printers. At the end of 2011 JMC Signmakers purchased an Esko Kongsberg i-XL44 with the corresponding MultiCUT and PowerHead. Cees Bolijn explained: “Not surprisingly the Kongsberg is considered the Rolls Royce of milling and cutting tables. The unique combination of MultiCUT and PowerHead makes it possible to process an extremely wide range of materials. This means that we can considerably expand our product range – a necessity in the current highly competitive market.
We manage to process many different orders, including PVC milled letters, clean cut paper posters in various formats, engraving on crystal clear polycarbonate and different types of wood, vehicle lettering stickers, a Re-board box, different corrugated cardboard boxes, clean cut magnetic plates, foam board posters, an MDF milled audio box, etc. For a company with so many different jobs in terms of materials and runs, automation is crucial.”
He continued: “The integrated camera vision recognition system measures the position and dimensions of the print before cutting, which guarantees an exact contour and less material waste. These tools enable us to be more creative and offer a wider range of products.” Even though this degree of automation was already a bonus, the three owners of JMC Signmakers recently decided to upgrade the hardware as well as the software, which means that a new ESKO Kongsberg C64 cutting table will be installed in due course. The main reason being, according to Cees Bolijn,: “We can now automate all the ‘dead ends’ in the system, going forward and knowing exactly what happens in the ESKO production system – all related to our own MIS solution.”
New ArtiosCAD Software for 3D Design
JMC Signmakers are also set to acquire the ArtiosCAD software from ESKO to design and prepare files for 3D jobs such as packaging and displays. Cees Bolijn: “Obviously this will be integrated into our system. If a customer orders a box and has an example in Illustrator, or provides measurements, we can import or describe the file in ArtiosCAD. This software can then produce a PDF template for the customer. ArtiosCAD can fixate some of the package measurements and change other parts independently. Of course it will also be fully integrated into the ESKO workflow environment. We will continue to work with Illustrator, for example, when variable data is involved.
Efficient Production
The way in which JMC Signmakers optimized the production workflow over the years is quite amazing. Different files are combined and split up, to generate increased production efficiency. JMC Signmakers processes 130 to 150 orders per week. Operators used to spend approximately 30 to 45 minutes on the separation and combination of an order. The company’s own software does it all in a flash. Cees Bolijn: “The software unravels orders and cleverly combines them with other part orders.
The machine only needs to be adjusted once and produces several products in a single run. Each part order is bar coded to ensure that the right products are allocated to each client.” JMC Signmakers is now able to switch very quickly because the order administration system is linked to printer and finishing equipment control software. Calculation of the possible combinations is almost instant. Bolijn explained: “In fact there are 81 different ways to produce the final product. Our software can quickly make the right decisions on how to produce a final product in the simplest, most cost effective way. Each material type, such as cutting foil or di-bond, and process type (sawing, milling, bonding etc.) is referred to as an item. Items are saved in the database as sequences of 0 and 1. Orders received by telephone or e-mail are immediately translated into a production order. With our automation model everything can communicate with everything on the basis of XML.” He continued: “We don’t want a print order to take much longer than 4 hours and production times should be kept to 48 hours. I mean 4 hours including installation and delivery in terms of work. You can imagine that margins are higher when we can offer our jobs within this time frame.”
Variable Data
The effective use of variable data to add value to marketing and promotion, in order to be closer to the customer, has been a subject for discussion for more than two decades. “In view of the fact that major brands are increasingly giving advertising a more regional appeal, not just at language level but even using dialects, and taking into account specific habits and/or religious persuasions, sign product personalisation is becoming a necessity.”
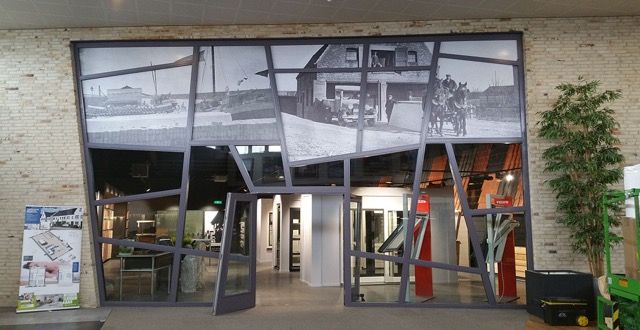
Cees Bolijn added: “But there was always failure in speed and production. With Extend Script for Illustrator, Photoshop and Indesign, we devel- oped a new technique to print variable data for large format print quickly and effectively. XML files are produced using an SQL server and then adopted by the Automation Engine with rules in Java script, as a result of which the Extend script is controlled.
JMC Signmakers has produced an Extend script generator, facilitating compact scripts that can easily be implemented to ensure that the PDFs that need to be printed are produced in no time at all.” He continued: “It can be used not only to personalise sign products but also, for example, for patterns in etched glass that have to be applied to different window formats or sign- posting involving numbers and text. Not only the ext, photographs and logos are variable, but also characteristics such as rotation (signposting arrows), colours, scales (proportional or not), positions with respect to other objects (relative or absolute) and processing (crop, filter etc.).”
Pre-production for Third Parties
Cees Bolijn quoted a typical example: “1,500 personalised banners, based on a selection of 11 designs of on average 70 Mb, with a unique name and run for each banner, are now arranged in 4 hours with the files nested and ready to print. What I like about the ESKO software is that it can easily be combined with my own programming rules to obtain highly sophisticated results.” Because JMC uses dye sub, solvent and UV in-house and offers appropriate finishing facilities, it can offer sign makers and designers a total personalisation package. Many sign companies spend a lot of time preparing files for signposting, large window lettering orders, exhibition sign- posting, etc. JMC Signmakers maintains that this new technique can produce significant cost savings, without JMC Signmakers necessarily carrying out the print order. The company can also handle pre-production and deliver complete production files to other sign makers enabling them to complete their orders.