Maryland-based Independent Can has migrated from the Nexus platform workflow to Esko’s advanced server workflow, Automation Engine, streamlining its operation, reducing errors, and automating prepress tasks for dramatic increases in productivity.
Founded in 1929, Independent Can is a world leader in the manufacturing of specialty decorative tins and metal lithography. Its product line has grown from the wholesaling of large cans for fresh and refrigerated foods to an extensive array of items serving a wide variety of markets, including custom-printed cookie, candy and popcorn tins. To uphold its company mission, “To be the best, not the biggest,” the company follows an unhurried and well-thought out plan of continuous investment and innovation.
Independent Can’s prepress department processes approximately 960 files annually, for printing on the shop’s KBA Metal Star six-color press with Trail UV Coater, the only one of its kind in the United States, or its Metal Star II four-color UV press. With two high-speed presses continually ready for action, time to market shrinking, and design files becoming increasingly complex, the need for a more robust yet simplified prepress workflow became apparent.
Automation Engine 10, the backbone of Esko’s Suite 10 packaging and print pre-production software, answered the call. The prepress server, installed at Independent Can in March 2011, provides high-level quality control and increased throughput and efficiency, simplifying the entire file management process and delivering extensive automation for job tracking and prepress functions. Pre-setting of repetitive tasks, such as trapping and step-and-repeat, result in reduced operator manual control and reduced errors.
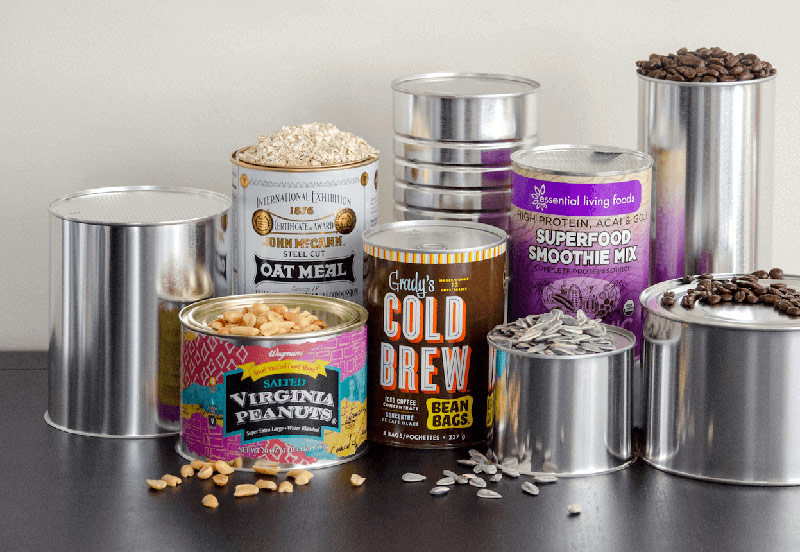