Reynders Achieves Significant Operational Efficiency Gains with CDI Crystal, XPS Crystal and Automatic PlateHandler
Changing market dynamics and unpredictable fluctuations in demand meant simplification of a manual platemaking process was needed to boost efficiency at Reynders.
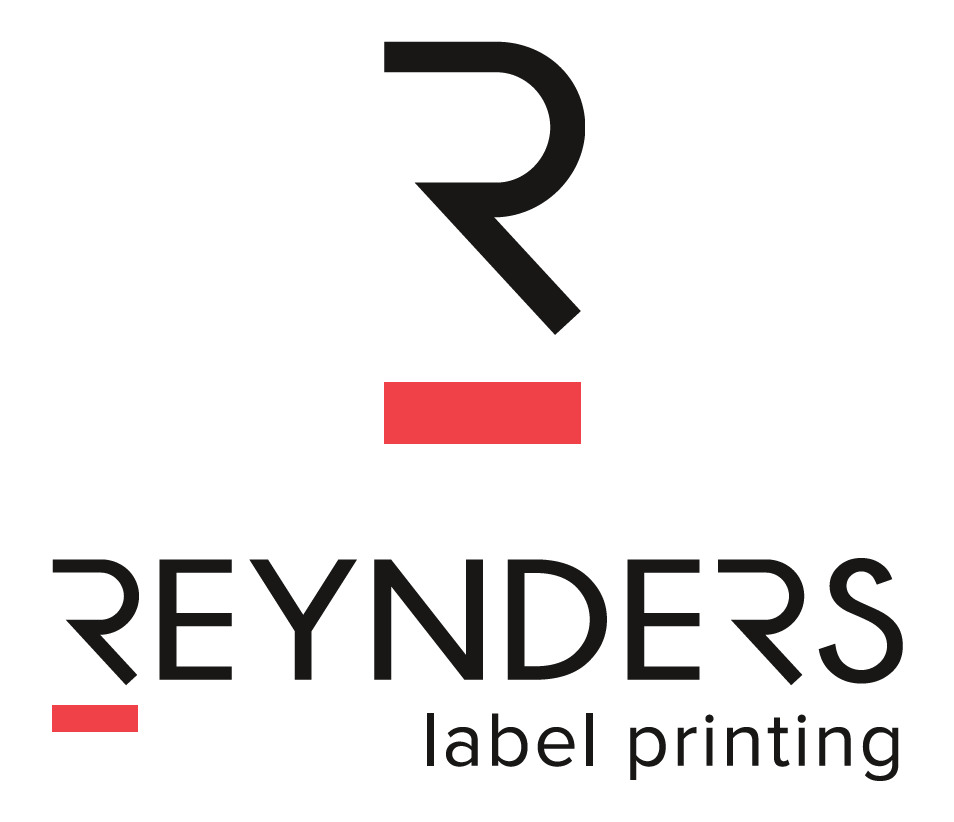
The Customer
Eight billion labels per year
Established for over 60 years Reynders is a leading international label printer headquartered in Boechout, Belgium. With over 500 employees located across seven sites in five countries in Europe and Asia, Reynders prints over eight billion labels per annum.
With decades of experience in label printing, today the Reynders business successfully operates across the food and beverage, pharmaceutical, cosmetic, industrial, automotive, chemical and household products markets. Producing self-adhesive labels, sleeves, flexible packaging and in-mold labels, the business has diversified over many years and developed a core culture of hyper-efficiency; but enhanced with a personal touch for customers. Consistency, standardization and centralization are the keys to the business’ success.
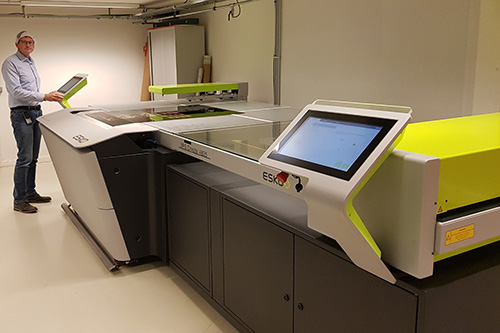
The Challenge
A manual plate-making process hinders prepress operational efficiency and flexibility
While Esko Automation Engine operates as a central workflow server for the Reynders business, enabling digital prepress files to be moved smoothly around the company’s sites, the prepress platemaking process at the Boechout site had become outdated, explains André Vandepitte, Prepress Manager.
“2020 has been a very strange year with unpredictable fluctuations in demand due to the Covid-19 pandemic. However, we have been very fortunate at Reynders. Being a key supplier to the surging food and beverage and pharmaceutical markets, we have seen increased demand for our label products and have been very busy. Fortunately, about a year ago, we had invested in a range of Esko hardware which galvanized our ability to service this growing demand in our prepress department.
“Here at Boechout, we supply both our French and Belgian businesses with flexographic plates and were operating with an old Esko CDI with two exposure units. However, our plates are very small – being in the label printing business – and there were multiple manual steps required in completing a single job, causing significant manpower inefficiencies.
“We had to move a plate four separate times to complete the imaging and exposure process between the various pieces of kit and then finally transfer them over to the wash out process. This was laborious and took a lot of our operators’ time just moving plates around. In addition, our exposures were inconsistent. With the old lamp system, we were constantly having to check, measure and control performance to get the plate quality we needed. Essentially we were wasting a lot of time in non-value adding work and not getting the capacity we were looking for.”
We’ve gone from moving plates from machine to machine, to a streamlined, integrated and automated process that simply takes the push of a button to operate.
Prepress Manager, Reynders, Belgium
The Solution
Reynders invests in Esko CDI, XPS & Automatic PlateHandler to speed up plate production and further boost quality
In 2019, Reynders invested in a new Esko CDI Crystal, XPS Crystal and Automatic PlateHandler for an impressive reduction in complexity in the Boechout plate room. The new imager is designed to connect seamlessly with the XPS Crystal digital UV exposure device. Combining high resolution fibre laser imaging with the patented back and front UV LED exposure from the XPS Crystal produces digital flexo plates with unique reproducibility and quality.
In addition, Reynders took the step to invest in Esko Automatic PlateHandler. The new Automatic Plate Handler provided the opportunity to create a touchless plate production process through to wash out, securing valuable gains in operator time and platemaking efficiency. A robot connecting the CDI Crystal with the XPS Crystal, the PlateHandler reduces the number of operator touchpoints and the costs of operation. Integrating the flexo plate making equipment frees up 50% of operator time to attend other and more valuable tasks, such as quality control, plate storage or plate mounting.
Our operators are freed up to concentrate on value-adding jobs and we’re now able to run at one person per shift, which is a lot more cost effective and efficient.
Prepress Manager, Reynders, Belgium
The Benefits
Plate quality and consistency are further boosted, and operators are freed up to work on value-adding tasks
“Investing in an integrated suite of platemaking hardware has completely simplified our process. We’ve gone from people running around, moving plates from machine to machine, to a completely streamlined, integrated and automated process that simply takes the push of a button to operate,” said André.
“Bringing the Automatic Plate Handler into the equation has meant that our operators have a lot more time on their hands. They are freed up to concentrate on more value-adding jobs and we’re now able to run at one person per shift on our two-shift system, which is a lot more cost effective and efficient.”
“Importantly, we’re also seeing far more stability in our plates. Instead of constantly having to check whether lamps are warmed up correctly, or fixing problems, we now have consistent output from the XPS Crystal and don’t need to worry. This too has freed up time for our operators, not having to constantly check and measure the output of the lamps as the LEDs are simply on or off!
“Of course, with over 50 flexo and digital presses to feed across the Group, prepress can become a real bottleneck if not managed efficiently. We’ve had a very long relationship with Esko and they were the obvious choice when it came to investing in our prepress capabilities. The integrated nature of what we have today means we have the quality, consistency and capacity in platemaking to not just meet – but exceed – the needs of our customers day in, day out.”
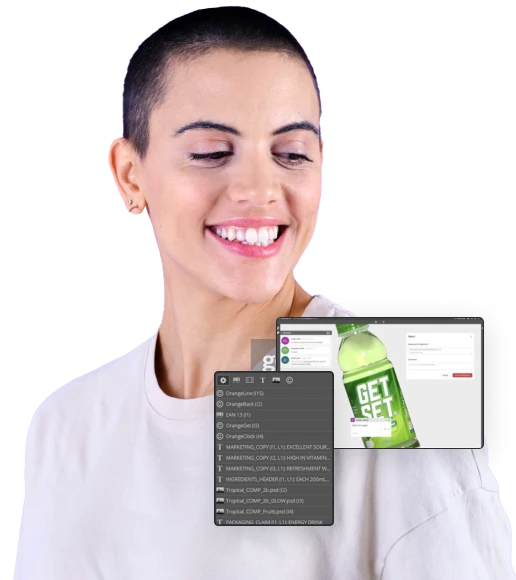