Glatz Klischee Reports Highly Consistent Flexo Plates with XPS Crystal 5080
Austrian prepress service provider Glatz Klichee marks a technology milestone with the award winning flexo plate exposure device XPS Crystal 5080.
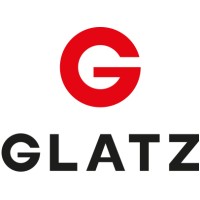
The Challenge:
Glatz Klichee felt that traditional light tube exposure units have reached their limits in the plate making process. There were problems with consistency or variations in exposure intensity.
The Solution:
XPS Crystal 5080, Esko’s flexo plate making exposure device
The Benefits:
Improved plate exposure quality and extremely consistent flexographic
plates. Even small print points and delicate screen structures are better placed with back exposure than before, and the reliefs are extremely consistent.
Case Study Summary
A crucial step in stable and consistent flexo plate making is UV exposure. That is the reason why Austrian prepress service provider Glatz Klischee installed Esko’s flexo plate making exposure device, the XPS Crystal 5080.
Benefits include:
- Improved plate exposure quality and extremely consistent flexographic
plates - Even small print points and delicate screen structures are better placed with back exposure than before, and the reliefs are extremely consistent
- A constantly uniform output thanks to UV LED exposure
- Adjustable intensity of the UV radiation according to the requirements of the job
About Glatz Klichee
As part of the Glatz Group, Glatz Klichee GmbH is a prepress service provider in Bregenz, Austria. The company specializes in flexible packaging and corrugated cardboard in Austria, South Germany and Switzerland. The product range includes corrugated cardboard, flexible packaging, plates and coating plates for offset print. Glatz Klichee prides itself on its highquality production of flexography up to 250lpi screen and strives to guarantee the best quality in plate making.
In our opinion, UV main and back exposure in one unit represents a milestone in flexographic plate making. It improves plate exposure quality and ensures extremely consistent flexographic plates.
Managing Director of Glatz Klischee, Austria
Early adopter of UV LED exposure
Glatz is a prepress service provider in Bregenz. It prides itself on its high-quality production of flexography up to 250lpi screen and strives to guarantee the best quality in plate making. It felt that UV plate exposure was a weak link in the process and that traditional light tube exposure units have reached their limits.
As a result Glatz Klischee investigated Esko’s LED exposure as early as 2010. Since then the trade shop has gained experience with several generations of inline UV exposure and worked with prototypes of the XPS Crystal 5080. Even in the early stages it could clearly see the potential of the Esko solution.
We are realizing that, in terms of quality, especially with very fine 250lpi screens, back exposure is more important than previously assumed. Even small print points and delicate screen structures are better placed than before, and the reliefs are extremely consistent.
Technical Manager at Glatz Klischee, Austria
Back and main exposure in one process
“In our opinion, UV main and back exposure in one unit represents a milestone in flexographic plate making. It improves plate exposure quality and ensures extremely consistent flexographic plates”, says Manfred Schrattenthaler, Managing Director of Glatz Klischee.
Glatz Klischee has been working with the new XPS Crystal 5080 from Esko for about six months now. The fact the new solution delivers main and back exposure in one step – has proven to be a huge improve- ment in device development and is on the point of making a quantum leap in plate manufacturing.
“Thanks to this technology, we now are able to supply our clients with standard screens (137lpi/152lpi), up to the absolute premium range with 250lpi. We can deliver the best possible plate quality with the highest level of consistency and repeatability that we have not experienced to date”, remarks Manfred Schrattenthaler.
An important process advantage in this new plate making approach is the fact that Esko has brought back and main exposure together in one step: “We are realizing that, in terms of quality, especially with very fine 250lpi screens, back exposure is more important that previously assumed. Even small print points and delicate screen structures are better placed than before, and the reliefs are extremely consistent”, says Holger Stier, Technical Manager at Glatz Klischee.
Thanks to this technology, we now are able to supply our clients with standard screens (137lpi/152lpi), up to the absolute premium range with 250lpi. We can deliver the best possible plate quality with the highest level of consistency and repeatability that we have not experienced to date.
Managing Director of Glatz Klischee, Austria
Disadvantages of light tubes
Glatz Klischee reports that LED exposure eliminates the disadvantages of traditional light tube exposure, which is widely adopted in flexography. There are no more problems with consistency or variations in exposure intensity as the XPS Crystal 5080 ensures a constantly uniform output. Glatz Klischee also likes the fact that not only the duration of the exposure can be controlled, but also that the operators can regulate the intensity of the UV radiation according to the requirements of the job.
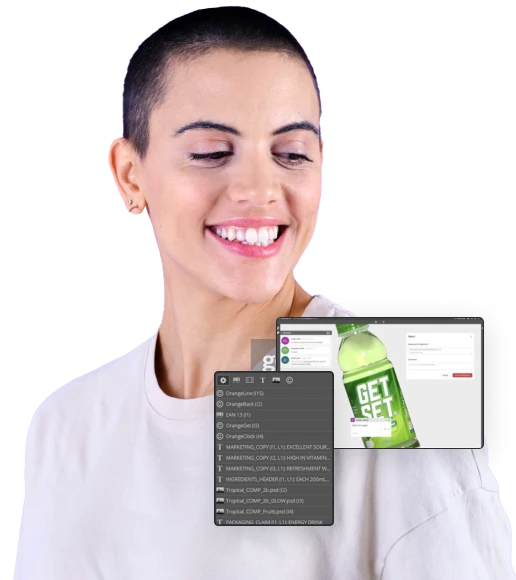