Albéa maximizes efficiency and improves customer collaboration with WebCenter from Esko
Leading cosmetics packaging manufacturer embraces digitalization to deliver customer satisfaction and efficiency gains.
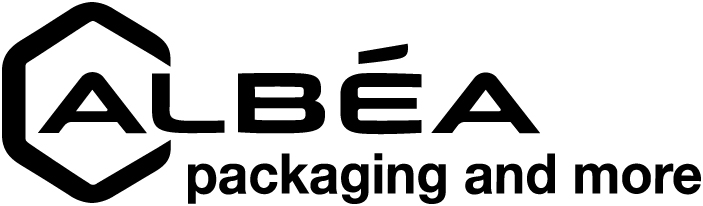
The Customer
Albéa, Gennevilliers, France
Albéa is the world’s number one cosmetic packaging wholesaler, manufacturing packaging and beauty solutions from tubes and lipsticks to mascara, applicators and much more. As a beauty packaging supplier, Albéa serves both established, leading brands as well as those companies emerging into the market at national and international levels.
The company benefits from 31 manufacturing sites across 13 countries, as well as working with partner suppliers in other countries. Albéa has secured its worldwide client base and reputation through ensuring high-quality manufacturing, operational performance, high-level logistics monitoring and management of complex projects – as well as market-value innovation and a recognized commitment to Corporate Social Responsibility.
Taking great pride in the fact that innovation is at the heart of its success, Albéa manufactures innovative products that offer better ergonomics, visual differentiation, affordable prices and fashionable design. The company also embraces innovation in its processes, developing new technologies and processes to set its packaging apart and make it effective, more competitive and more environmentally friendly. It does this while rising to its customers’ technical challenges and ensuring design objectives are met at the right cost.
Digitalization makes it possible to rapidly increase production at various sites in different countries, and in some cases to make supplies more flexible and secure
New Product Launch Director with Albéa
The Challenge
Increasing flexibility without compromising efficiency
“The ever-changing demands of the consumer coupled with the competitiveness of the sector means that our customers are constantly seeking shorter lead-times and smaller order sizes,” said Valérie Lebelt, New Product Launch Director with Albéa. “With strategies that demand multiple launches, visual differentiation and meeting sustainability goals, the cosmetic tube market was already experiencing upheaval – and this has only been compounded during the recent coronavirus (COVID-19) crisis.
“To address these increasing demands, Albéa is revolutionizing the development process for our leading products, embracing digital technology as a part of the solution to deliver increased flexibility,” said Valérie. “We recognized if we were to continue to meet our customers’ requests for agility, responsiveness, innovation and reliability, digital technology was the answer. Digitalization of our processes would make it possible to speed up certain technical stages while at the same time making them more reliable. It would also enable us to manage projects in a more collaborative way, and to ensure end-to-end transparency throughout the lifecycle of a project.
“Digitalization makes it possible to rapidly increase production at various sites in different countries, and in some cases to make supplies more flexible and secure,” added Valérie. “On a technical level, digital printing delivers many advantages in terms of speed of execution, agility and personalization, which is all very attractive. But we know that in practice, buying a digital press is not enough. The result can only be reliable if the upstream process is mastered, and that’s where working with Esko became so important.”
WebCenter delivered the ability to not only effectively manage our project portfolio, but to also deliver higher levels of efficiency, easier and constant prioritization and therefore optimal responsiveness to our customers
New Product Launch Director with Albéa
The Solution
Collaborative, efficient, controlled prepress processes
“We worked closely with Esko to develop prepress tools as well as a collaborative platform to manage projects within our industrial facilities, across our various sites and also directly with our customers and their design agencies,” said Valérie. “Esko WebCenter delivered the ability to not only effectively manage our project portfolio, but to also deliver higher levels of efficiency, easier and constant prioritization and therefore optimal responsiveness to our customers.”
WebCenter is a powerful packaging management and collaboration platform that allows for companies of all sizes to digitize their processes and meet today’s challenges head on. The secure, web-based software has been tailored to help packaging converters meet the demands of a rapidly changing business environment.
Managing all aspects of preproduction specification, approval and project lifecycle to remove the most common bottlenecks in the packaging design to production process, WebCenter is the only solution on the market specifically developed for the packaging industry. The integrated approval process shows when an asset was sent for approval, who the approver is, and when it is approved, before the software then automatically and seamlessly triggers the next tasks – and all in real-time.
“The time to market factor is becoming increasingly important to our sector,” said Valérie. “Only a few years ago, the acceptable expectation was that the process could take around three months for a new product, but today the expectation is that we can deliver in just four-to-six weeks. With WebCenter, we are able to reduce our time to market while fully controlling the quality of execution of the project.”
Only a few years ago, the acceptable expectation was that the process could take around three months for a new product, but today the expectation is that we can deliver in just four-to-six weeks. With WebCenter, we are able to reduce our time to market while fully controlling the quality of execution of the project
New Product Launch Director with Albéa
The Benefits
Flexibility with quality assured through standardization
“The flexibility WebCenter delivers in terms of prioritization and responsiveness has been a critical asset throughout the global crisis,” said Valérie. “It meant that as a business we would not be immobilized by the disruption of a particular supplier or a given country. Instead, we had the flexibility to adapt quickly to any sudden changes in the market; the ability to switch production across sites in line with supply chain constraints and opportunities.”
Valérie explained that by going digital, Albéa had eliminated the requisite adjustments at the end of the line, but this in turn had generated new needs upstream, in the prepress stage of production. “Since we always have to go faster, we have to make sure we have mastered the prepress stage, along with color development and the design of the tools,” she said. “Control of the entire graphic chain is therefore both a quality and time to market issue. Esko has become a true partner in the digital transformation of our printed packaging development process.
“One example is how color sequence standardization is included in a digital file,” she explained. “This file allows us to provide a proof to our customers – a rendering that is similar to a print trial made on industrial equipment in our sites – but that is actually made off-line on small digital printers that are calibrated for each type of tube.
“Our customers always receive a real sample, and the ability to maintain that process has been particularly important throughout the pandemic,” said Valérie. “Obviously, the various restrictions we’ve all been subject to have restricted travel and the ability to meet face to face, so being able to achieve speedy approval via email and post has helped bring us significant savings,” she said. “Whereas a traditional color proof, made on site with an industrial line, can take anywhere from four to six weeks and use 300 kgs of plastic materials, with WebCenter at the heart of the proofing stage it now only takes a few days and uses just 150g of resins. This is two thousand times less material, which generates significant savings as well as reducing the impact on the environment.”
Valérie said the deployment of WebCenter would continue across the business and would be particularly useful in the new product development process. “Our collaborative and secure platform will also be open to our customers,” she said. “They will be able to interact directly with our experts – not only to preview the rendering of their design but also to validate the whole tube development, including the color of body and cap.
“This will mean that developing a new tube becomes a collaborative, efficient, fast process, which also saves time, money, plastic and reduces carbon emissions.”
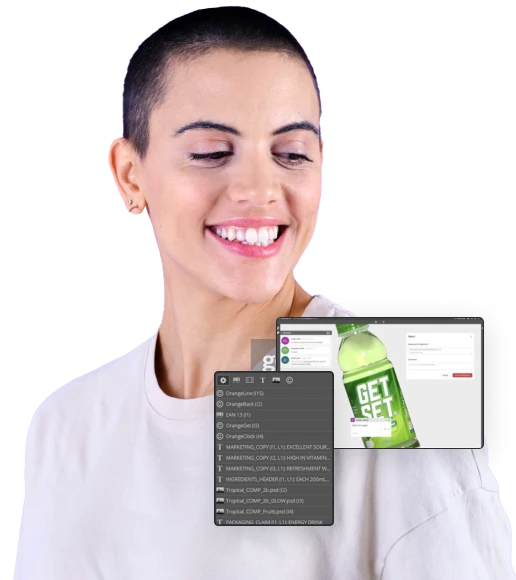