Polytec Optimizes Print Quality with Esko Print Control Wizard and XPS Crystal LED Exposure Unit
Leading flexible packaging manufacturer benefits from unparalleled platemaking consistency, increased efficiency and reduced ink consumption with Esko Crystal technology.
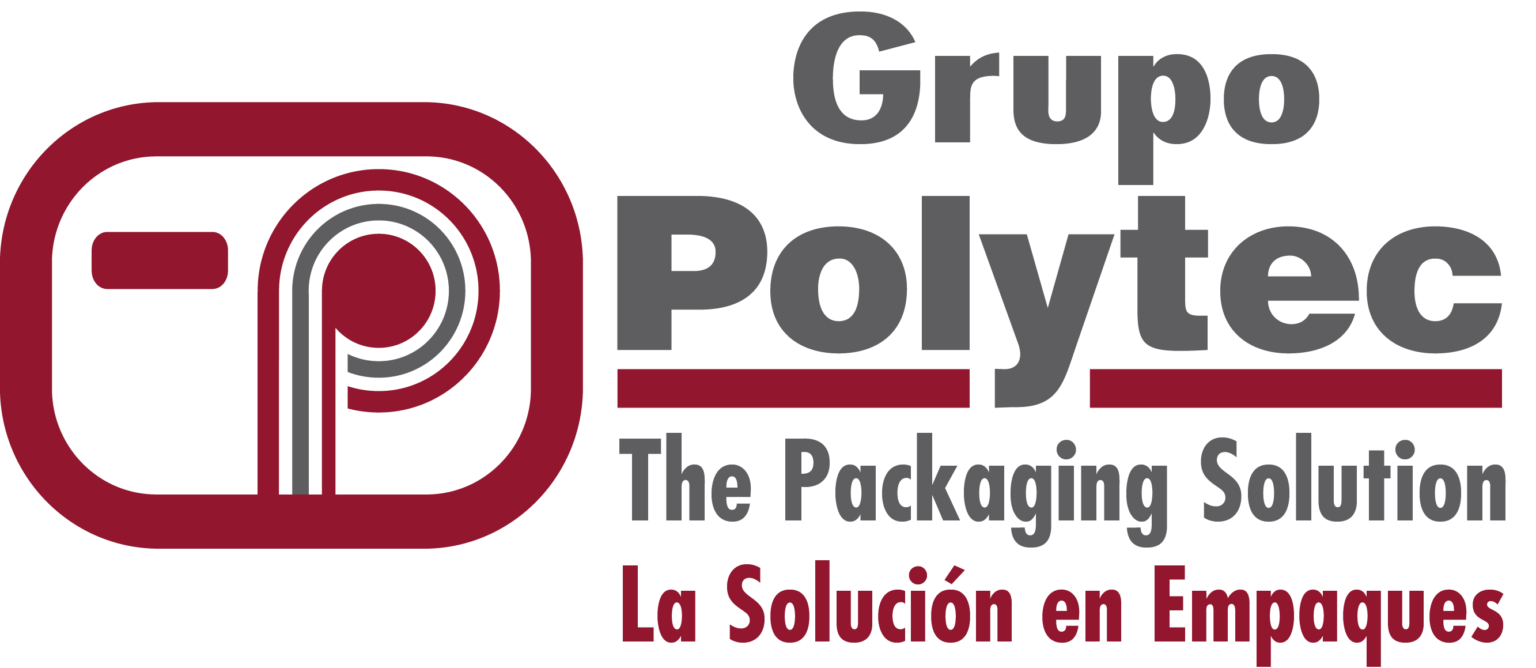
The Challenge:
Improve surface screening for whites and enjoy greater control over printing profiles.
The Solution:
Optimize print results by integrating Esko Print Control Wizard into existing flexo operation.
The Benefits:
Consistent plate quality, control of highlight tones and reduced ink usage.
Case Study Summary
Founded in 1989, Polímeros y Tecnología, (‘Polytec’) has grown from its beginnings as a flexible packaging manufacturer for the local market to an international supplier with seven flexo presses and a monthly output of more than 2,500 tons.
With customers across the food and drink, detergents and agriculture sectors, the company’s 750+ workforce has established a reputation for expertise in every aspect of flexible packaging production from extrusion, printing and laminating through to slitting and bag making.
- Reduced makeready times.
- Achieve right color on press in less time.
- Improved accuracy and consistency.
- Savings on white ink consumption.
Standardized processes, improved results
“After acquiring the Esko XPS Crystal 4835 exposure unit – which uses front and back UV LEDs that always emit consistent heat – we wanted to take full advantage of its new Crystal screen technology capabilities,” said Augusto Guerra, Prepress Manager with Polytec. “We knew that with Esko Print Control Wizard, we could really unlock the potential of our XPS Crystal and enjoy advantages in surface screening for whites and more control on making printing profiles.
“By incorporating Print Control Wizard into our automated platemaking setup, we were immediately able to harness the power of the XPS Crystal to improve our white ink opacity and appearance,” he said. “We have standardized our procedures so we can develop printing profiles in a very professional way, and we are now also on our way to reducing white ink consumption.”
Accuracy, consistency, efficiency
Augusto said the Polytec team was already familiar with Esko and its prepress and flexo platemaking solutions, with the company using an integrated ecosystem of Esko software such as Automation Engine, PackEdge and Imaging Engine, as well its CDI flexo plate imager and XPS exposure unit.
“The combination of Print Control Wizard and the XPS Crystal has delivered remarkable platemaking consistency, with superb control of highlight tones,” added Augusto. “With this, we have been able to reduce our makeready times, achieving the right color on press in less time. This improved accuracy and consistency means we also hope to save on white ink consumption, further adding to the efficiency gains.
“Esko is a world-class company, with all kinds of sophisticated solutions for prepress, and that was what we needed.”
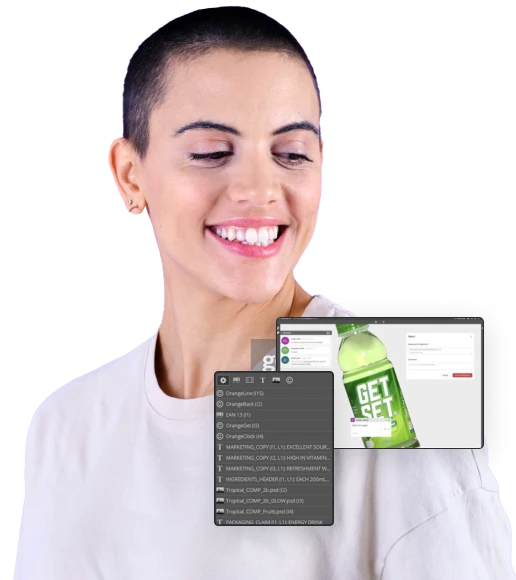