Imprimerie Ste-Julie Uses Esko Crystal Solution to Increase Agility and Produce Bigger, Better Quality Plates in Less Time
Leading Canadian packaging and labels company Imprimerie Ste-Julie was looking to ramp up its plate production, without compromising the quality of its finished print. With a need to deliver bigger plates in reduced lead times, the company identified Esko as the perfect partner to support them!
The Benefits:
Increased agility, increased speed.
The Customer
Imprimerie Ste-Julie, Quebec, Canada
Imprimerie Ste-Julie has been defining standards in the label printing and shrink sleeve printing industry for more than 40 years. Founded in 1975 in Quebec, Canada, Imprimerie Ste-Julie leads and is always innovating to offer different print options to its customers for their packaging needs. The company now has more than 120 employees and boasts state-of-the-art equipment manufacturing self-adhesive labels, shrink sleeves, pouches and label booklets, with either flexo or digital print and a range of added value finishes.
With clients across Canada, Imprimerie Ste-Julie serves a range of markets, from food and pharmaceuticals through to alcohol and cosmetic products. The business has built a reputation for delivering on the promise of its four corporate values, ensuring that every project is carried out with passion, quality, customer focus and agility.
Customers choose Imprimerie Ste-Julie for the quality of its products, speed of execution, and commitment to customer service, while the variety of options it offers positions the company amongst the leaders in the field.
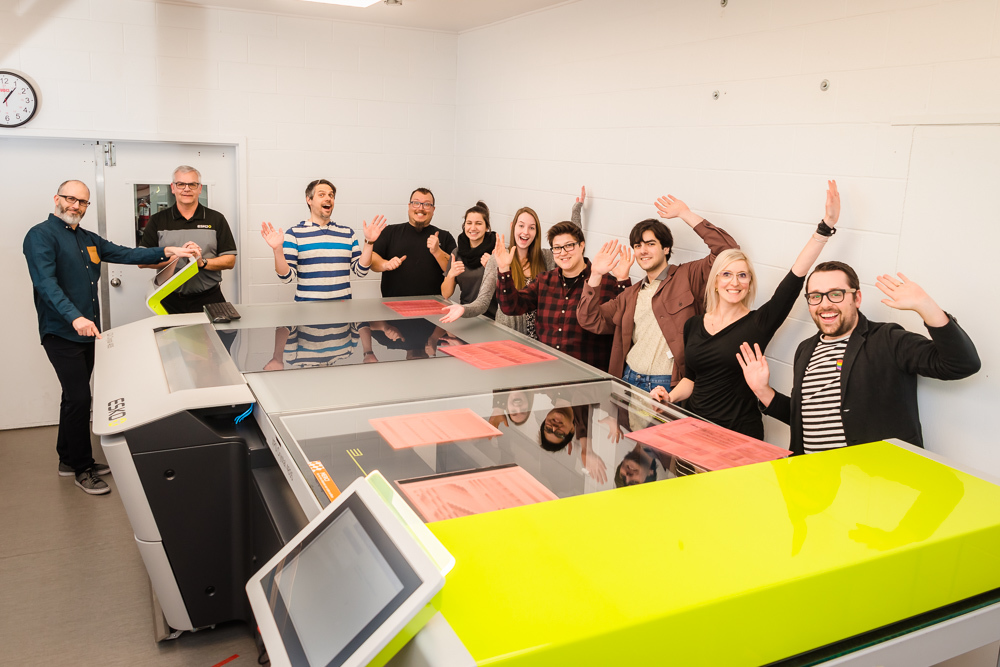
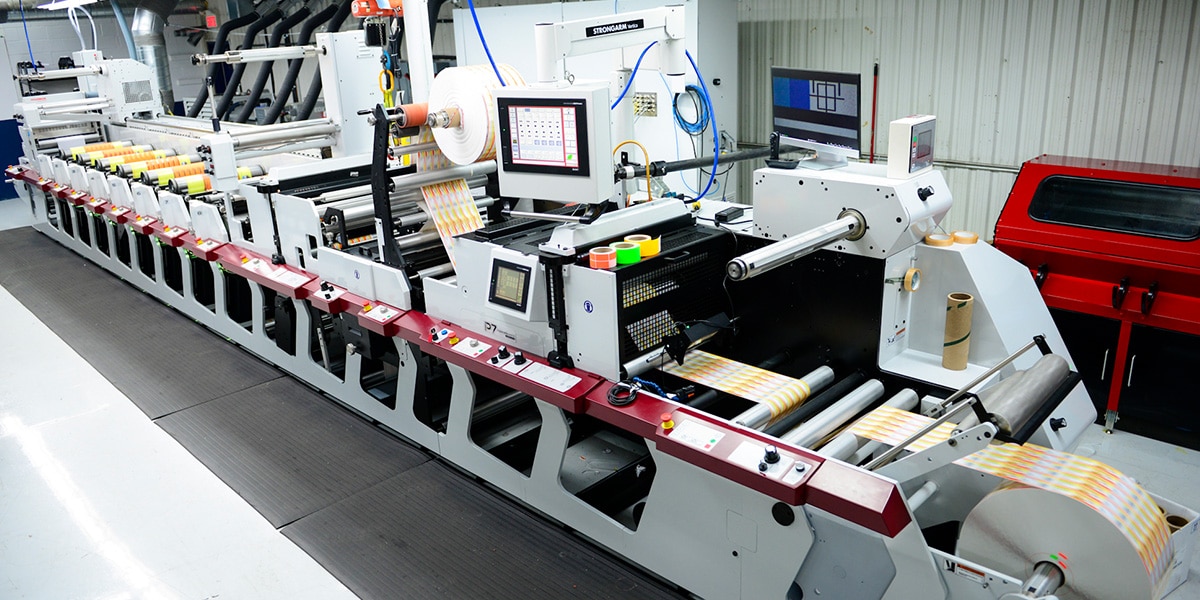
The Challenge
Speed, accuracy and quality
“Competition has always been, and will always be, fierce when it comes to quality and production lead times,” said Simon Dumais, Prepress Manager with Imprimerie Ste-Julie. “Our biggest challenge is always to maintain the quality of our print, while ensuring production speeds that meet market demand.”
“We needed to produce more large plates on a daily basis, and we identified that our old machines and software installations were presenting an obstacle to achieving this. We chose Esko as our business partner as we knew they offered the most complete range of products to meet our needs and would allow us to offer turnkey options and optimal service, which is very important to us. In addition, Esko offered a solution for the automation of our prepress processes, something which is essential for us in meeting the quality and speed expectations of today’s market.
“It is important for us to be able to standardize and automate our operations in order to avoid errors in files or at the production stage,” added Simon. “Moreover, we wanted to ensure everything was interconnected, enabling us to avoid errors in data management. This level of automated connectivity then frees up precious time for us to be even more customer service oriented.”
We use the system several times daily and it is now an integral part of our production process
Prepress Manager with Imprimerie Ste-Julie
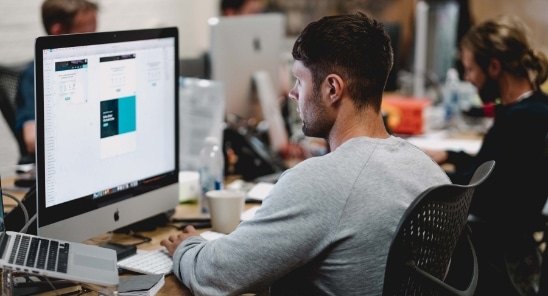
The Solution
The Esko Crystal plate making system
Imprimerie Ste-Julie has produced its own flexo plates on site since 2007, bringing manufacturing cost benefits and efficiency gains through production speed gains. An Esko CDI Crystal XPS integrated imager and exposure solution was installed in September 2019 in the graphic arts department, where 13 specialized employees work across the graphic design and prepress processes.
The combination of a CDI Crystal flexo imager with an XPS Crystal exposing unit offers a perfectly integrated flexo platemaking workflow. With UV main and back exposure, the XPS Crystal uses LEDs which require no warm-up time and emit even light, producing excellent consistency of plate quality and subsequently on press. The CDI Crystal XPS offers efficiency and quality gains such as reducing manual steps by 50%, reducing operator time by more than 70% and less plate and time waste through reducing errors by 50%.
“We wanted to develop our customer experience while also continuing to develop that of our employees,” said Simon. “Thanks to the complete Crystal system from Esko, it is now not only much simpler and faster to produce our flexographic plates, but in addition we also enjoy improved quality in the final print. We use the system several times daily and it is now an integral part of our production process, particularly given the constantly reducing lead times we are seeing.”
As well as the Esko CDI Crystal XPS, Imprimerie Ste-Julie has invested in Esko Automation Engine, an automated workflow server, as one of the central tools in its operations. “Automation Engine imports information from the command software,” said Simon. “We have then added Proof Pack for our color solutions, the CDI and the XPS Crystal for the manufacturing of our flexographic plates, as well as other tools that allow us to work with variable data and make 3D models of containers for proofing of shrink sleeves and various printed products.
“Thanks to this acquisition, we no longer have any constraints on speed and quality, either in prepress or production.”
Thanks to this acquisition, we no longer have any constraints on speed and quality, either in prepress or production
Prepress Manager with Imprimerie Ste-Julie
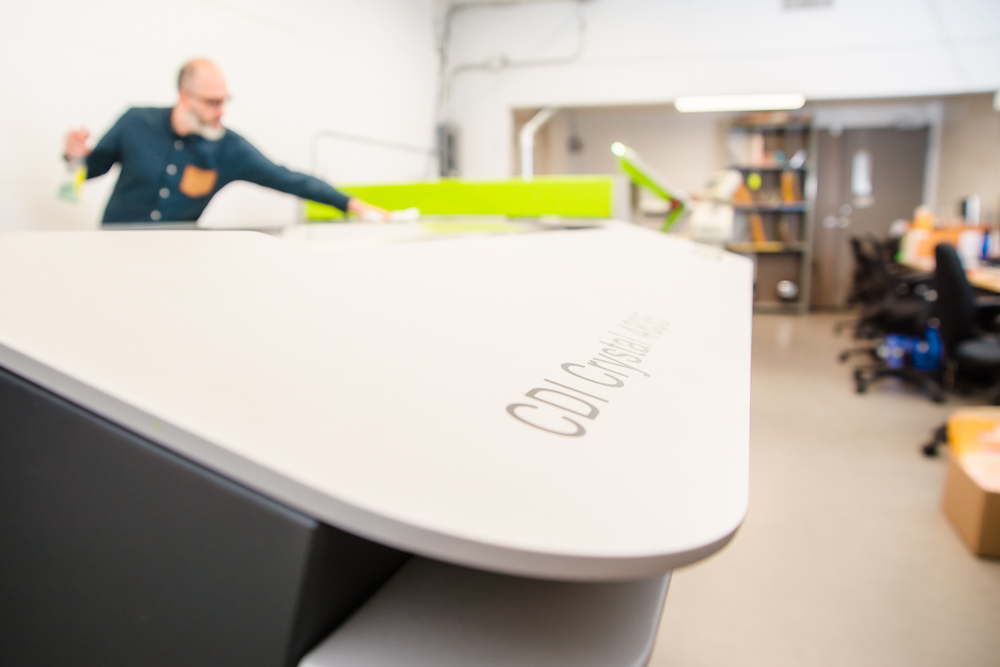
The Benefits
Increased agility, increased speed
“The main benefit that the Esko CDI and the XPS Crystal bring to our company is that we now have the capacity to produce superior quality plates with increased speed,” said Simon. “This allows us to be more agile in our response to growing customer expectations for surprisingly short delivery times.
“Importantly, thanks to Esko Pixel+ high definition software technology combined with the Crystal XPS system, quality is no longer an obstacle to speed,” he said. “In addition, the production of our flexographic plates takes 66% less time than with our old equipment. This is very important, because it allows us to respond more quickly to our customer demands or to redo one or more plates for a press that is stopped. Also, being able to work with larger plates allows us to easily meet demand for our 20” wide press, while still feeding all of our other presses, avoiding downtime and waste.”
Simon said that the quality and efficiency of the Esko system had proven very impressive. “The consistency of the floors and reliefs, and the definition of the points of our plates, prevent a lot of waste and press stop times caused by defective plates,” he said. “We are more than satisfied! This technology allows us to have flexographic prints that are as beautiful, if not more beautiful, than digital prints. The colors are always vivid, and the gradients are perfect!”
The system is now fully operational, helping Imprimerie Ste-Julie continue to deliver on its promise of completing every job with passion, quality, customer focus and agility.
The production of our flexographic plates takes 66% less time than with our old equipment
Prepress Manager with Imprimerie Ste-Julie
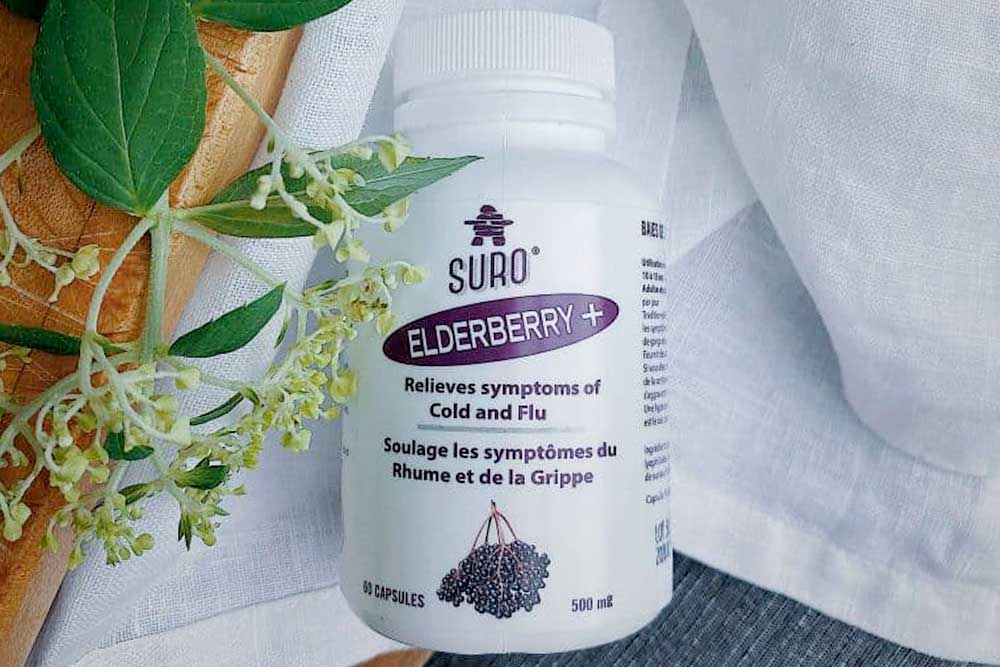
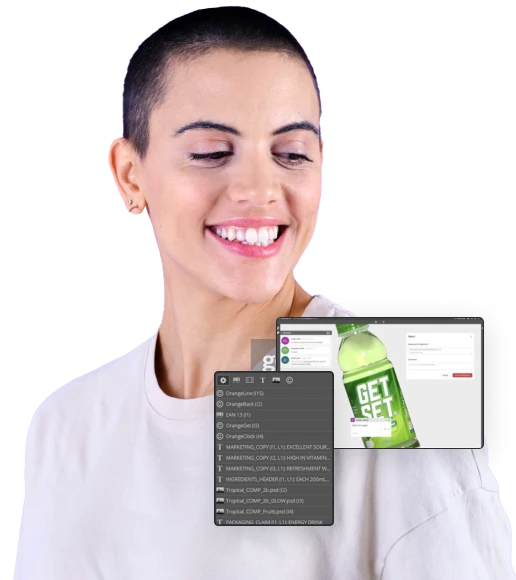